A wide variety of applications use copper braid as it is a versatile material. There are many braids available; however, your application’s needs will decide the type of braid you will need. This blog post will give you a clear idea of different braided copper wire types and their use.
Table of Contents
What is a copper braid?
A copper braid is a structure weaved through copper wire strands. The diameter determines the flexibility of the braid. When the diameter of the copper strands is small, flexibility is high, volume is large, and the braid becomes more expensive.
Conductor Braids
Conductor Braids refer to the braids in which small strands of wire braid together to form a conductor. The wire is flexible, and you can use types of materials to form the braided wire. Copper is the most common, either bare or coated, depending on the application. Tinned copper braid is the most common, with good conductivity, resistance, and soldering capability. Additionally, there are silver-plated and nickel-plated copper braided wires.
The making of the braided wire starts with the multiple strands of thin wires that wind on fast-rotating spools. The rotating spool incorporates the wire together in a circular pattern around a core into a string and flexible braid.
The carriers in the braiding machine determine the wire size. It is a crucial part of a braiding machine that serves different purposes. It holds the wire bobbin, maintains control when the wire breaks, and compensates for the difference in length while keeping the tension constant.
A braiding machine can have 16, 24, or 48 carriers depending on the machine, and each carrier has a bobbin where each bobbin can hold 1-16 wire strands or maybe more.
You can determine the number of carriers and wires in a carrier through a three-number identification system on the construction information of a braid. In this three-number identification, the first indicates the number of carriers, the second shows the number of wires in one carrier, and the third number indicates the gauge size of a wire. For example, if the identification number is 48-11-30, the number of carriers is 48, no. of individual wires in a particular carrier is 11, and the gauge size is 30.
Round (tubular) braid
Most industrial applications use round braids. Round braids increase the amount of space in the small cross-sectional area of the cable. As a result, such cables can fit in panels and machine openings where flat cables are difficult to fit.
In addition, around braid offers corrosion resistance, impact resistance, and protection against electric fields. It has stranded construction and good conductivity to handle a wide voltage range.
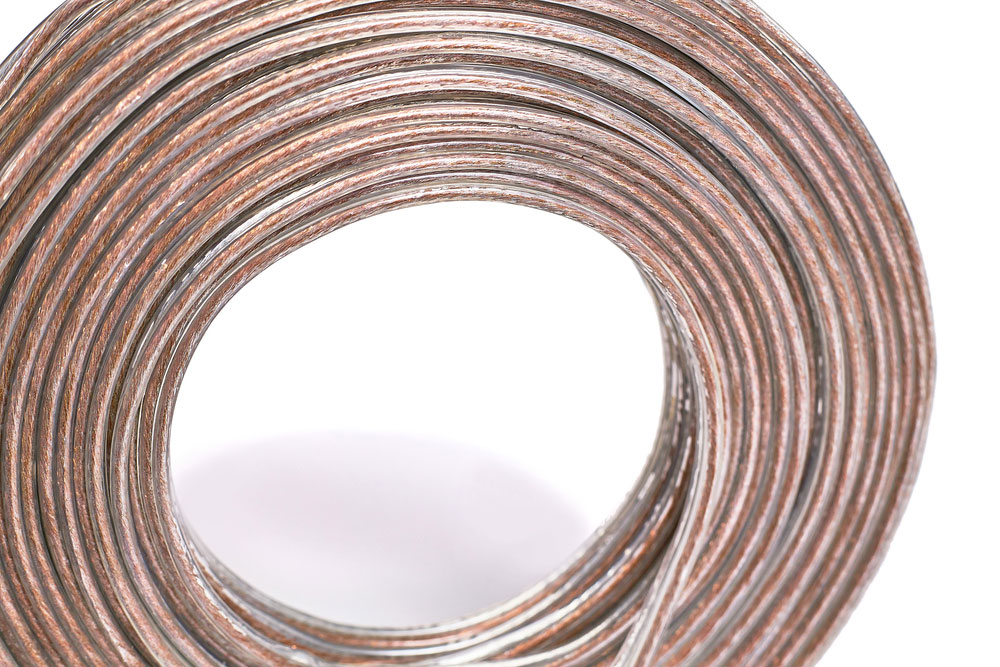
Image: a coil of braided copper wire
Flat braid
You can use flat copper braids in medical, Civil-aircrafts, and semiconductors to supply power and data to the machines. During their manufacturing, flat braids start as round braids, but then manufacturers apply pressure through a roller on a capstan to make them flat.
Flat braids are similar to round braids in flexibility and strength. However, these braids have a larger surface area, which shows less resistance when electricity passes through them. Further, it has low inductance.
You can use the flat braid in industrial and commercial applications. Due to their ability to absorb shocks and vibration, you can use this braid for grounding. They can also be used in broadcasting applications.
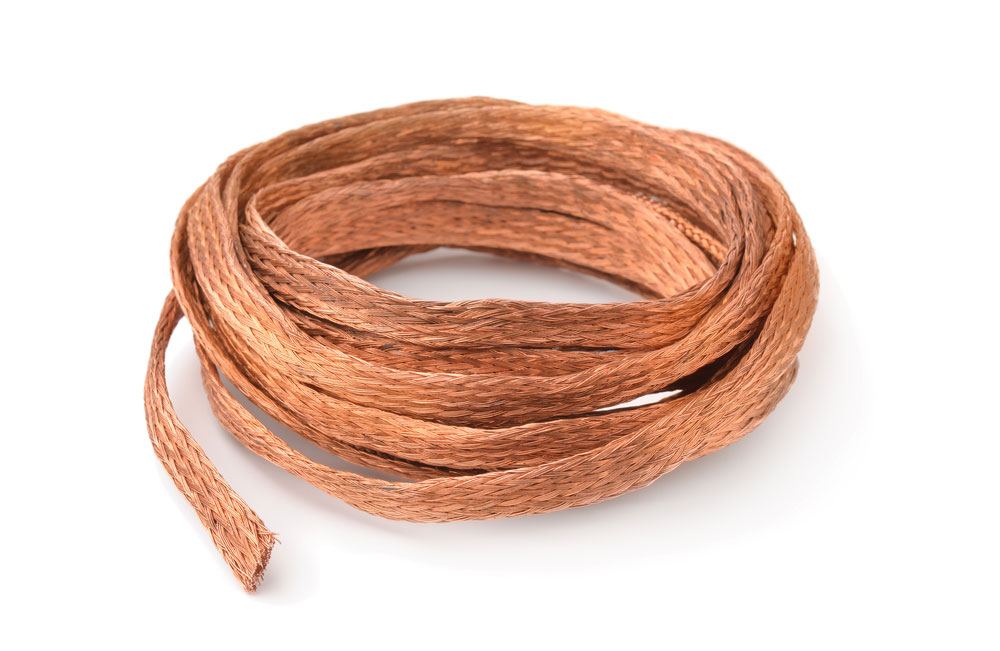
Image: flexible copper braid
Shielding braids/tubular braids
It refers to several fine wires that tighten and weave together to form a meshed tubular structure that wraps around a conductor. Usually, tubular braids can be flattened to achieve a specific width. You can also use an overtop, a thin insulating layer, to offer additional protection to the braided wire and conductor.
Shielding braids serve two purposes.
- Firstly, to protect cables from electromagnetic interference.
- Secondly, to increase the mechanical strength and flex life of the cables.
The most common materials used for tubular braids include tinned copper and silver-plated copper.
Why is braided wire necessary?
Smartphones, radio waves, and natural light are everywhere. Electromagnetic interference is the biggest hurdle in electrical circuits, causing data loss and electrical failure. When using an interwoven shield, the wire deflects the EMI frequencies (low to medium frequencies) and keeps signal strength and reliability. Secondly, the design of the braided shielding enhances the cable’s flexibility.
What’s the difference between braided wire and foil shielding?
Foil shielding is the metallic tape that protects cables against high frequencies. As foil shielding does not have lattice formation, it folds or kinks cables, while braided shields make the cable more versatile.
Braided wires have several advantages, but you cannot necessarily use them in all applications. Braided shielding offers only 70-90% of the internal components’ coverage and makes the cable bulky. Thus, it is unsuitable for tight space areas or applications requiring 100% coverage.
Braided copper Assemblies At Gloom
At Bloom, we offer a wide variety of braided cable assemblies such as round braids, tubular shielding braids, flat braids, and knitted copper mesh that suit a variety of applications. We have a vast supply chain to deliver large quantities cost-effectively and a guarantee of performance.
Earth Straps and Bonds
These are highly flexible connectors and leads that you can use in building services, switchgear, and ATEX environments. All in all, you can use our earth straps and bonds in various vibration applications.
High voltage copper braids
Transformer braids and copper braid busbars are a perfect solution for the renovation of grids, stand-alone power units, and UPS, as these are quite flexible.
We supply copper braid connectors for connecting busbars to bus ducts, transformers, gen-sets, UPS systems, generators, switches, isolators, circuit breakers, fuses, ACBs, MCCBs, and other electrical connections in a power transmission system. You can use these copper braided busbars in high-strength electrical connections.
Conclusion
You can send us your requirements. We deal in a series of metal braids, such as copper braid products that can work in a wide temperature range. Our engineers will guide you to the most appropriate design based on your application’s current capacity, operating temperature, and dimensional constraints.