You generally use soldering and resistance welding methods for wire splicing because they are trusted and reliable solutions in many applications. Compared to soldering, you prefer resistance welding in applications with nickel or steel or where the bundle of wires is too small. However, the biggest drawback is high heat generation, damaging the spliced materials. Another issue is that it causes high electrode wear, which operators must pay regular attention to. On the other hand, soldering is also a good solution but has drawbacks. For example, it is challenging to have tight control of the process, and in areas where the temperature is too high, you cannot trust the integrity of the spliced ends. A better option, ultrasonic wire splice, is becoming popular in new applications, especially in automotive.
Table of Contents
- What is ultrasonic welding?
- What is an ultrasonic welding machine?
- What is the Process of ultrasonic welding?
- In-Depth Look at Ultrasonic Wire Splice
- Two types of Ultrasonic Wire Splicing Machines
- How does Ultrasonic Wire Splicer work?
- Ultrasonic Wire Splice Parameters
- Ultrasonic Wire Splice Quality Variables
- The Types of Ultrasonic Metal Welding Products
- The requirements of the ultrasonic metal welding process
- The advantages of Ultrasonic Wire Splice harness welding machine
- Conclusion
Table of Contents
- What is ultrasonic welding?
- What is an ultrasonic welding machine?
- What is the Process of ultrasonic welding?
- In-Depth Look at Ultrasonic Wire Splice
- Two types of Ultrasonic Wire Splicing Machines
- How does Ultrasonic Wire Splicer work?
- Ultrasonic Wire Splice Parameters
- Ultrasonic Wire Splice Quality Variables
- The Types of Ultrasonic Metal Welding Products
- The requirements of the ultrasonic metal welding process
- The advantages of Ultrasonic Wire Splice harness welding machine
- Conclusion
What is ultrasonic welding?
The ultrasonic welding process uses high-frequency ultrasonic vibrations around 20 kHz to 40 Khz to join two thermoplastic pieces. Converting HF electrical energy into mechanical motion, the plastic material forms a molecular bond after melting.
What is an ultrasonic welding machine?
To understand the working principle, you need to understand all its parts.
Machine press
You use this to hold the welding system and apply force. It has a base plate holding the cooling jig and a pneumatic cylinder that exerts pressure. You can adjust the welding force through a pressure gauge or regulator.
Generator
The generator converts electrical energy from the primary source (Single phase) to the needed voltage and frequency. After this, the transducer converts this electrical energy into mechanical vibrations. The welder gets the necessary communication through the microprocessor unit of the generator.
Welding stack
The welding stack provides the required ultrasonic vibrations. It mainly has three parts, the booster, welding horn, and transducer. You can mount all three elements at the center of the machine. The welding stack frequency must match the generator’s electrical energy.
Transducer
In a transducer, several piezoelectric ceramic discs lie between two titanium blocks. There is a metal plate between the discs, which acts as an electrode.
Booster
Booster has two roles; firstly, it amplifies the mechanical vibrations and transmits them to the welding horn. Secondly, you use it as a base for stack mounting, and the booster expands and contracts to amplify the vibrations.
Welding horn
It transmits the energy to the workpieces which will be welded. It is made from aluminum or titanium, where you can only use aluminum for low-volume applications.
Supporting tooling
As the name suggests, this tooling supports all the workpieces while welding and firmly holds the components when high vibrations are applied.
What is the Process of ultrasonic welding?
Let’s delve deeper into each process to understand them in detail.
Step 1: Parts in the fixture
Here you must put two thermoplastic parts that you need to weld together on top of each other in a fixture.
Step 2: Horn Contact
Bring an aluminum or titanium component to the upper side of the plastic part. You can call this component a horn.
Step 3: Application of pressure
Then, apply controlled pressure, so the parts clamp to the fixture.
Step 4: Welding
Now, vibrate the horn vertically at 20khz to 40khz times/second for a specific weld time. The parts have a precise design, so the energy reaches specific contact points between the two regions.
The thermoplastic materials transfer mechanical vibrations to the familiar interface and generate high frictional heat. The temperature reaches the melting point and starts melting plastic. It would help if you stopped shaking. As soon as you stop vibration, plastic will begin cooling.
Step 5: Hold Time
You must maintain the clamping force for a specific period so that parts fuse once the plastic melts and solidifies. This clamp holding duration is hold time. If you want better joint strength or an airtight seal, you can apply a higher force during this period.
Ultrasonic Wire Splice: Step 6: Horn Retracts
Once the plastic melts, you can remove the clamp and retract the horn. Now, you will see that two parts join as if they are molded together.
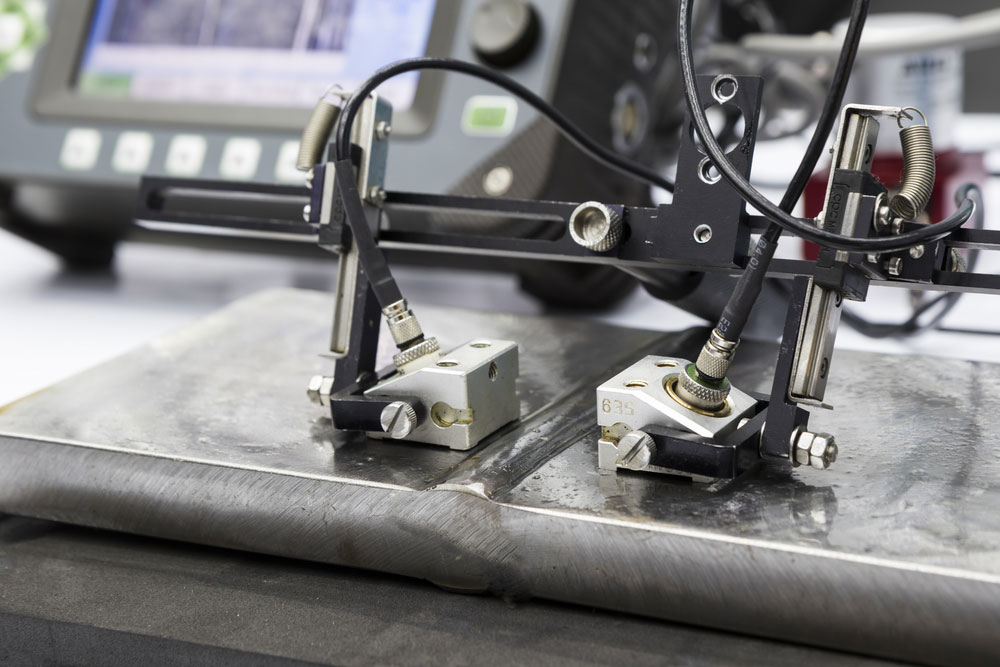
Image: ultrasonic probe testing welding steel
In-Depth Look at Ultrasonic Wire Splice
You can witness the high growth in the automotive industry these days with everything becoming electro-mobile. Ultrasonic welding is the most successful and reliable joining process. Manufacturers from different sectors, including transportation, aeronautical engineering, and others, use this technology for splicing and terminating wires to connectors.
Ultrasonic connections have low electrical resistance, excellent protection against corrosion, and are cost-effective. Manufacturers also use them in prefabrication, producing cable harnesses on the assembly board and solidifying individual wires strands. Nowadays, you can also link recent wire splicing systems to the users’ MES or manufacturing execution systems to increase reliability and improve quality assurance.
In the era where welding systems are becoming flexible, for example, combining copper to copper or copper to aluminum requires welding with the same machine. You will also find special tools for multiconductor and twisted cables.
Two types of Ultrasonic Wire Splicing Machines
You can choose either of the two types of metal and plastic welding methods.
Linear welding: All equipment manufacturers use this common technique of welding.
Torsional welding: It came into the picture only a decade ago. You can use this technique in most of the applications of linear welding. Telsonic developed it. Due to the advantages of its delicate process and applications’ geometrical shape, you can use it in a broad spectrum of applications. It is the only technology you can use for electric car battery manufacturing and terminating high voltage cables. Other applications include 3D terminals and IGBT (Integrated gate Bipolar Transistors).
How does Ultrasonic Wire Splicer work?
Firstly, stack the wires between the sonotrode and the anvil block. Sonotrode is the oscillating tool. Ensure that the device and block remain in a confined space before you apply the force through the anvil. When the oscillation starts, the metal surface begins heating and melting. As a result, wire strands form a bond by intermixing plastic parts. Finally, you will get a fine-grained structure.
The vibration due to force helps dispel any impurities and triggers the cold friction welding until the splicing continues. The temperature rise in the welding material is 30% less due to friction force. As a result, the wire does not harden, making it brittle. It is the main advantage of ultrasonic welding technology over resistance welding.
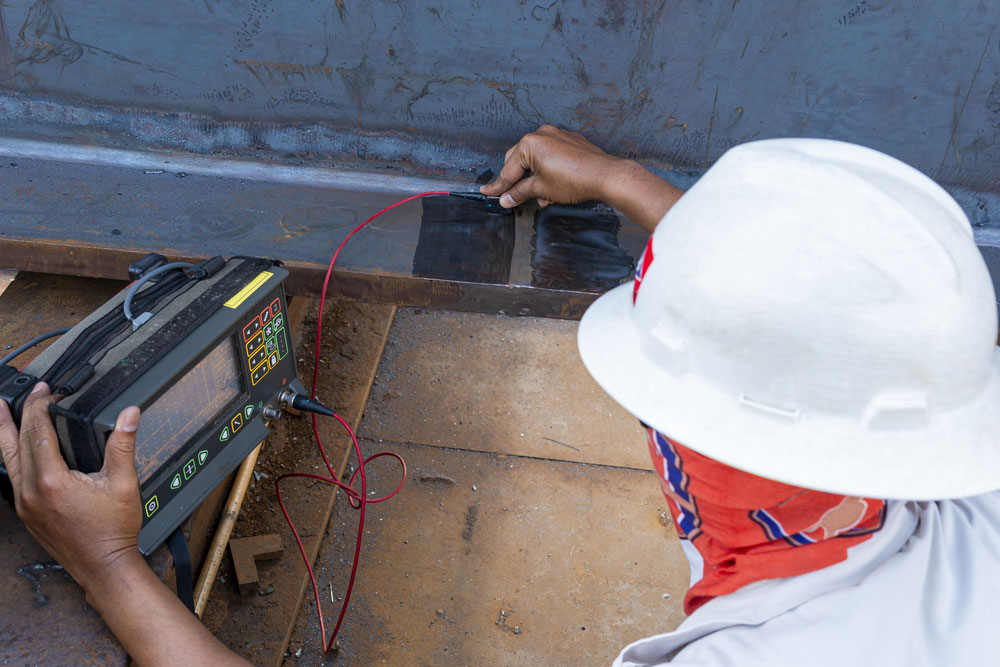
Image: inspectors checking defects in welded steel with ultrasonic testing.
Ultrasonic Wire Splice Parameters
The Ultrasonic wire splicing is safe and of high quality as you can adjust the parameters according to the requirements of your applications.
- Weld width: machine sets this up.
- Weld energy refers to the watt/seconds required for weld completion.
- Amplitude refers to oscillation, which you can adjust up to 100% depending on the sonotrode capability.
- Force-pressure setting: you need it to set the welding force.
Ultrasonic Wire Splice Quality Variables
When welding with fixed energy and controlling the process to get the best quality welds, you can measure and compare the following variables with their upper and lower limits.
- Weld time, i.e., duration of welding
- The final height of the weld
- Consumed power
- Measurement of compaction before oscillation starts
Some features can enhance the product’s reliability in wire splicing.
- Firstly, ensure that the machine stores all the splice data in a local network for future quality analysis and audits.
- Secondly, ensure that the panel PC is connected to UPS, so there are no issues during voltage drops.
- Thirdly, save the last spliced data to ensure the integrity of the system software.
- Monitor the splicing unit pneumatics.
Further, the wire slicing systems also support various options to enhance the products’ ergonomics and the operator’s convenience.
- A multiconductor splice kit handles the materials well to avoid rejected parts.
- Also, there is a cutter for bad parts that can destroy wrong splices.
- The modern splicing system can interface with the shrink oven to ensure the usage of correct shrinking parameters/splice.
The Types of Ultrasonic Metal Welding Products
The ultrasonic metal welding process helps to join multiple wires to each other. Additionally, you can join wires with high-current contacts and grounding terminals. The cross-section of the wire you can weld ultrasonically ranges from 0.08 sq. mm to 200 sq. mm.
You can use this process in splicing stranded copper wires in sub-assembly operations, compacting single wires, and final assembly of cable and wire harnesses.
Ultrasonic metal welding processes are of two types:
- Bilateral welding
- Unilateral welding
Based on the welding method, you can classify the process as:
- Embedding: as the name suggests, embedding means squeezing the metal part into the plastic hole with pressure.
- Riveting: it involves riveting two objects with the help of a vibrating welding head. The head presses against the protrusion, so it thermally fuses to the rivet.
- Spot welding means welding two objects with no clearly defined welding line.
The requirements of the ultrasonic metal welding process
Here are some conditions for automotive wire harness welding machine ultrasonically:
- Make sure that wires are not tinned or galvanized.
- The welding machines must-have software with reasonable quality control to give judgments after each weld.
- The wire head fixture gap should be ≦0.02mm as a significant gap can result in the stuck wire.
- You can use ultrasonic metal welding machines for welding metals like copper, nickel, gold, silver, or aluminum.
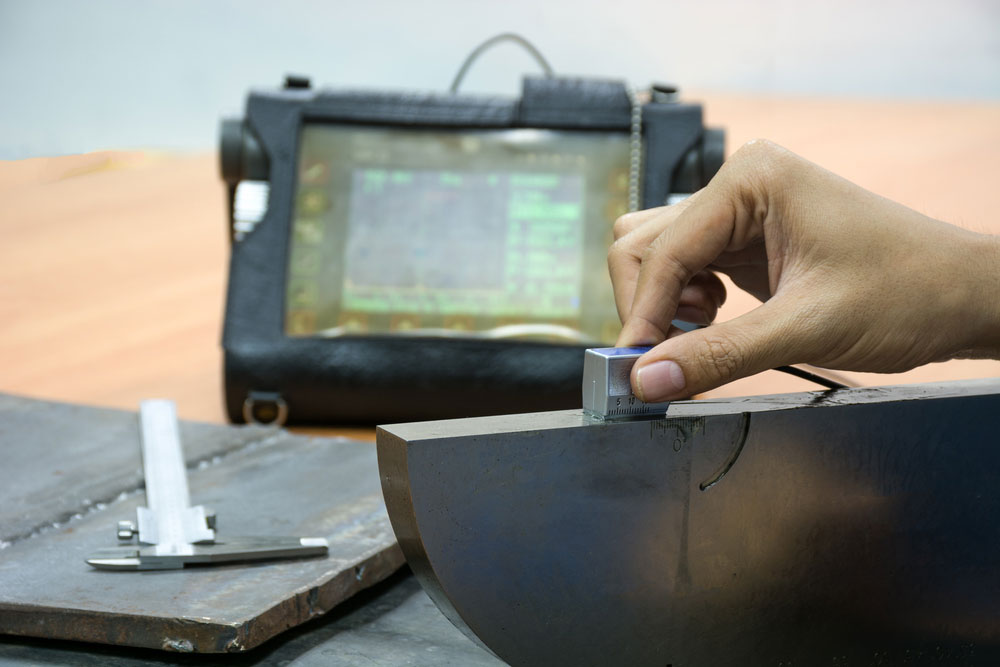
Image: welding inspection for ultrasonic test for internal defect
The advantages of Ultrasonic Wire Splice harness welding machine
Wire harness welding manufacturers in the automobile industry are getting inclined toward this process due to the following benefits:
- After ultrasonic welding, you will notice high compactness and lesser voids.
- This welding has nearly zero resistivity and higher conductivity. It also improves durability.
- It does not accumulate heat, which otherwise can increase temperature and cause the burning of metal parts.
- No external factors like dust, moisture, oil, or gas can affect ultrasonic welding. Also, it does not rust and oxidizes quickly. In other welding methods, environmental damages lead to poor electrical conductivity and slower signal transmission.
- Here, the welding temperature remains up to 50% of the melting point of the weld metal. As a result, the metal structure has no temperature effect or change.
Conclusion
Wiring harness manufacturers are gradually identifying the benefits of ultrasonic welding during assembly as it is fast and forms a highly reliable metallurgical bond within a fraction of a second. It is easier to manage data, consumes lesser energy, and is a cost-effective technique. If you need any help regarding the ultrasonic welding process for any application, contact Cloom. We are leading manufacturers of various wiring harnesses and cable assemblies for different industries.