As you are working on a project, there are types of areas that require different kinds of wirings. One of them is welding cables that, due to their durable nature, are ideal for many applications other than welding. Let’s dig into the welding cables and how you can use them.
Table of Contents
- Welding Applications
- What is Welding Cable?
- Similar Cables with Welding Cables
- Welding Cable Applications
- Choosing the Right Welding Cable
- Conclusion
Welding Applications
The two most common electric welding methods are resistance and arc welding methods, according to NEC 2014. You will use the welding cable to power the electrode in both welding methods.
Resistance Welding
High-current electricity with lower voltage is transmitted between two electrodes, and the metals are welded together. When you weld the two metals, heat forms due to the components’ resistance, and heat is utilized to connect them. As a result of the heat generated by the metals resisting the current flow, they are fused.
Arc Welding
A welding power source generates an electrical arc between the tool and the workpiece. The weld can be completed using only the metal left over after the electrode melts under the influence of an electric arc. Moreover, to sustain the turn, you must blow inert gas like argon gas between the weld and the electrode.

Caption: Arc welding
What is Welding Cable?
As per NEC 2014, the cables you need to connect the secondary circuits of the welder are welding cables. These cables usually have fine strands of copper that make them flexible, ranging from 8 AWG to 500 Kcmil in size. Moreover, they have EPDM rubber insulation with an operating temperature range from 90 degrees to 105 degrees Celsius.
Welding cables can easily resist the weld splatter due to their thermoset nature. They are typically rated for 600V, although you can find the ones with a 100V rating. Since welding cables are flexible, they are much more durable on rough surfaces where there is a need for repetitive movements.
Conductor of Welding Cables
The welding cables of class K have multiple stranding of pure copper that is 30 AWG. These cables have good flexibility and will not bend. Each strand is 0.00001 inches wide. Since the conductor has many tiny copper fibers, the best way to connect welding cables to devices is with crimped wire lugs and connectors.
Insulation of Welding Cables
Usually, the welding cables have a synthetic rubber called Ethylene Propylene Diene Monomer (EPDM) as their insulating material. EPDM rubber is very resistant to wear and tear. It doesn’t break down when exposed to solvents, greases, oil, moisture, water-based chemicals, or air. Additionally, it stays pliable over a wide temperature range and doesn’t shrink back much when you cut it.
Welding cables also have a piece of paper between the wire and the insulation. It reduces the friction between the wire and the insulation while working with the line.
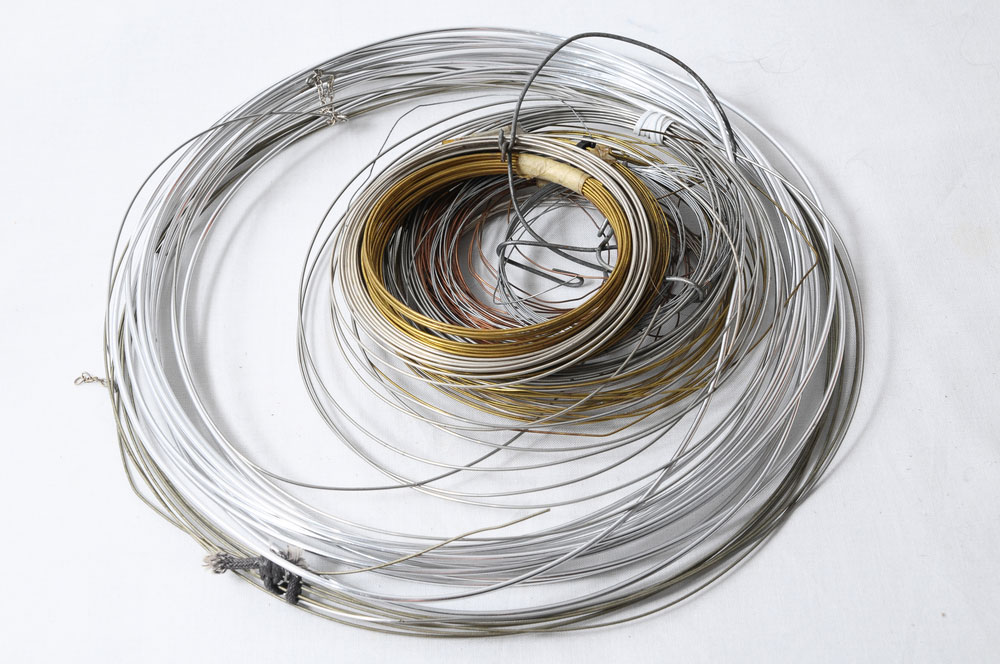
Caption: Metal Welding Cable
Similar Cables with Welding Cables
In high-end applications, two cables are similar to welding cables. These are battery and DLO cables.
DLO Cable
EPDM insulation and CPE jacketing are used in the DLO, also known as a diesel locomotive cable. Compared to welding cable, it is more durable and can withstand up to 2000 volts. There are fewer but thicker wire strands in the conductor, making the line less pliable than usual. Thus, you can use the DLO cable for welding.
Battery Cable
Because the welding machine’s open-circuit voltage reaches the 60-volt rating on battery cables, they cannot be for welding. The wire has larger strands and is less flexible than DLO and welding cables. Also, the cable-connected batteries cannot be welded, but the welding cable can.
Welding Cable Applications
The primary usage of welding cables is to link the secondary circuits of DC and AC welding machines, particularly those with long leads that stay in one place. Also, you can use them as portable power lines as they can handle 600 volts.
In some places, the welding cables can replace the battery cables, especially when you need them for starting and pulling. However, you must ensure they are secure, so they don’t rub against the vehicle’s body.
Here are some recommendations for applying the welding cables
- Although welding cables are suitable for many applications, most of these cables still do not comprehend the standards. Thus, it is best to use the weld cables under expert supervision.
- Alternatively, you can use the diesel locomotive cables or Type W mining wires with fine strands.
- Some signal-conductor thermoplastic cables are best for control cabinets, machine tools, and internal wiring applications.
Caption: Welding Circuit
Source: https://www.fabricatingandmetalworking.com/
Choosing the Right Welding Cable
To get the most out of your welder, you must ensure it provides a good amount of voltage and current at the job site. Also, see if the size of the weld cable is big enough for the most current your welding machine can send.
As a rule, for welding at 250 amps, you’ll need a 2/0 AWG wire with an outer diameter of half-inch approx. Also, if you have long cords, remember that the voltage will drop, hurting the quality of your welding.
Now, let’s clear the relationship between several parameters.
Ampacity
Ampacity, current rating, or current-carrying capacity is the maximum current value that can pass without surpassing its operating temperature. If you exceed this limit, your machinery will burn out.
The ampacity of welding cables has a different calculation method than the other wires. It appears to have a more significant amperage than items like building wire or tray cable. However, these ampacity values are only applicable to welding purposes. Additionally, it is essential to consider the duty cycle, output power of the welder, and circuit length when selecting the optimum cable size for welding.
Maximum Current
A welder power source’s maximum current can draw while the power supply’s rated output determines the operation. However, you must ensure that the cable is large enough to withstand this maximum value.
Duty Cycle
A duty cycle determines the capacity rating of a welding point. It is the percentage of time a power supply can run at a specific output current level without going over its thermal limit. Increased duty cycles are implemented when output levels fall below 100% continuous output. You can find this information in two places: on the power source’s label or in the manufacturer’s instructions.
The type of welding equipment used can affect the duty cycle. It depends on the welder’s intended use, intensity, type of phase, single or three-phase, and voltage rating. Arc Welders in part two and Resistance Welders in part three of NEC 2014 Article 630 Electric Welders have distinct requirements for setting duty cycles and ampacity.
Welding Circuit
During a weld application, the welding circuit is the entire channel in which electricity will flow. This circuit often includes a power supply, electrode, electrode cable, and work cable/ground cable. The circuit length is computed from the combined lengths of the electrode cable and the work cable. Thus, the longer the line, the lower the amperage rating because of the added resistance.
Caption: welding cable sizes
Conclusion
The durability of welding cable makes it best for a wide range of applications. Specific parameters to choosing a suitable line for your usage include ampacity, gauge size, and maximum current capacity. Here at Cloom, we offer wiring harnesses and cable assemblies.