If you place a wire in an electrical setup, you want the most it can give. That includes lasting for as long as possible while maintaining optimal performance. Wire insulation is crucial to preserving the wire’s integrity and maximizing its lifespan. This guide reveals everything you should know about wire insulation. Start reading right away to learn everything about this topic!
Table of Contents
- What is Wire Insulation?
- Different Types Cable Insulation
- How to Remove Wire Insulation Without Cutting wire?
- Conclusion
What is Wire Insulation?

Caption: A photo of multiple armored copper cables
Insulation is a vital protective material around the cable. It’s non-conductive since it needs to resist electrical leakage. That way, the current from one wire doesn’t mix with that coming from other cables. Insulation should also protect the wire from heat, water, and other factors. It directly affects how effective and long-lasting the wire is, which makes insulation a crucial feature.
Different Types Cable Insulation

Caption: Different types of cables
The wire industry uses three main insulation types, and numerous subcategories are available. While choosing a suitable option, you need to consider various features, including physical, mechanical, and electrical properties. Here are the insulation types present across a wide range of industries.
Plastic
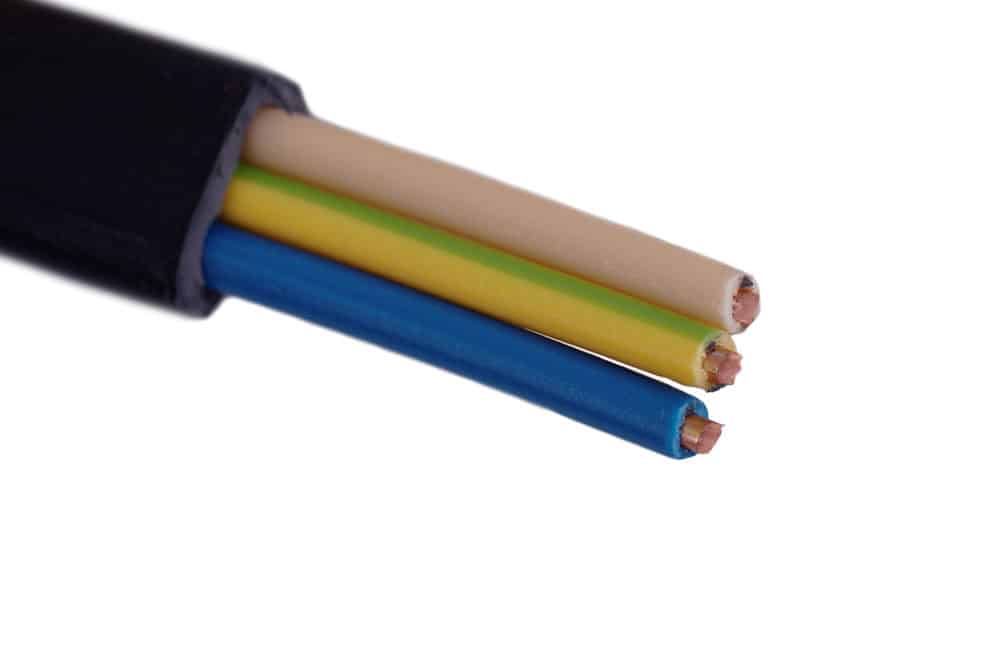
Caption: A three-core PVC cable
- PVC. It is an affordable material that’s easy to use, which makes it an efficient option. Its usable temperature range is from -55C to 105C. If you need a type for medical and food-related purposes, this is a good choice. PVC isn’t toxic, and it’s also tasteless and odorless.
- Semi-Rigid PVC. This variation has excellent resistance to water and flames, making it a frequent choice for primary insulation.
- Plenum PVC. Its physical properties allow use in areas where air circulates. The reason for its plenum rating is flame resistance that supports use at a wide temperature range.
- Polyethylene. You’ll often find PE in electrical applications that require minimizing the dielectric constant. The material is flammable, but it has decent electric qualities. It also has high solvent resistance, and it’s not easy to crack. Therefore, PE is a smart choice for low-voltage insulation in coaxial cables. Its temperature range is from -65C to 80C.
- Polypropylene. It’s a similar material to the previous one, but it has a thinner wall. Therefore, its temperature options go from -30 to 105C.
- Polyurethane. Military uses this material, and you’ll find it in retractile cord applications. It has impressive age resistance due to its excellent durability and toughness. PUR can handle freezing temperatures, but its downside is that it’s flammable.
- Chlorinated polyethylene. CPE has excellent weather resistance, and you’ll find it across various industries, such as power plants. This material is more eco-friendly than some other alternatives, and it’s more affordable than some other insulation materials for electrical wires.
- Nylon. The advantage of this material is its excellent flexibility, and it’s a durable option that works well in rugged environments. It doesn’t have high moisture absorption, which affects its electric qualities.
Rubber

Caption: A close-up of black electricity cable on a spool
- Thermoplastic rubber. If you need excellent heat resistance, you can’t go wrong with TPR. It’s also great for harsh environments, but it’s not resistant to cut-throughs. However, this thermoplastic material has a high-temperature range and processing speeds.
- Neoprene. It is a synthetic stretch of rubber suitable for an appliance wire. It has an excellent flex life, and it can handle cut-throughs, solvents, and abrasion. Furthermore, neoprene is remarkably flame-retardant, which is why the military uses it.
- SBR. It is short for styrene-butadiene rubber, which is similar to neoprene. It operates at as low temps as -55C or as high as 90C, and Mil-C-55668 cables often use it.
- Silicone. It’s an attractive option for its temperature ratings up to 180C, suitable for flex life applications. Furthermore, you can use it in an electrical appliance wire where you need bonding.
- Fiberglass. The range of temperature it can handle goes to 482C, making it a wise choice for glass insulation. While its abrasive resistance isn’t high, it can deal with chemicals and moisture. Aluminum processing has extensive applications where you can use fiberglass.
- EPR. High-voltage cables often come with ethylene-propylene rubber insulation. The material is flexible and soft, and its range of temperatures is from -50C to 160C.
- CSPE. You’ll find this in a motor lead wire and even transformer leads. Dupont registered this material as Hypalon. It can handle a wide temperature range, and it deals with UV rays well.
- EPDM. This synthetic material has excellent abrasion resistance, and its thermal endurance allows you to use it at heat levels from -55C to 150C. Furthermore, the material has high dielectric strength, and therefore, it’s an alternative to silicone as a cable insulation material.
Fluoropolymer
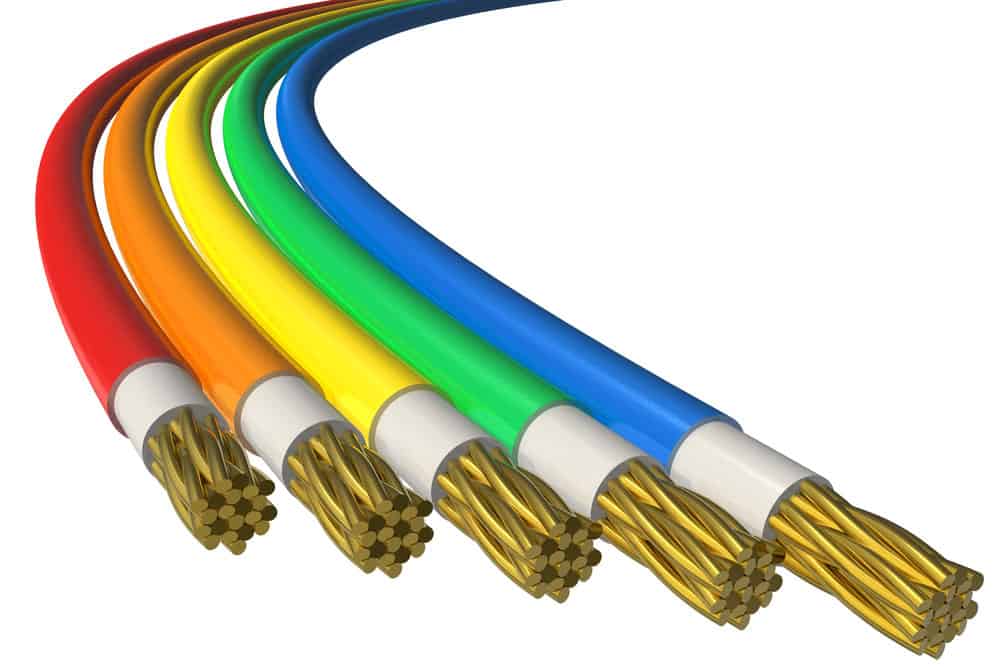
Caption: Power cables in different colors
- PFA. It has excellent mechanical properties, and you can use it at heat levels from -65 to 250C. Furthermore, the dissipation factor is low, which makes this material a great choice.
- PTFE. The resistance to oil and other factors make this another acceptable option, and the material is good at temps from -73C to 204C.
- FEP. You’ll find it in military applications, and it’s suitable for plenum areas. Furthermore, it’s a good choice for many wire sizes mentioned by the American wire gauge.
- ECTFE Halar and ETFE. It’s more robust and more flexible than previous materials. It can be a thermoset, and you can reduce weight by foaming. On the other hand, it doesn’t have great electrical benefits.
- PVDF. If you don’t want to pay much, this is a smart choice. PVDF has excellent ratings for its price, and it’s thermally stable, light, and flexible.
- TPE. This thermoplastic material is a mix of rubber and plastic. You’ll find it automotive applications, but it also has other uses. You can extrude or mold it, and it keeps a highly flexible level.
How to Remove Wire Insulation Without Cutting wire?

Caption: A close-up of an electrical wire
You can use multiple ways to remove insulation from the wire material. Therefore, it’s all about finding a method that suits you best. Here are the top suggestions so that you can pick your favorite!
Stripping Tools

Caption: A man using a wire cutter
If you have a stripping tool, you can use it to remove insulation. You’ll notice multiple notches for varieties of wires. Check to see if a notch matches your unit. You can use the numbers on the tool or check if it fits manually.
Put the tip of your copper wire into a suitable notch. Next, close the jaws and squeeze the tool. There’s no need to use too much force because the tool will do the job efficiently. Now, spin the stripping tool to remove the insulation. Finally, take it off the attachment of wires to finalize the process.
Utility Knives

Caption: Utility knives
You probably have experience with utility knives, but be careful during the process. First, put the wire on a flat and firm surface. Now, use the knife to cut the insulation slowly. Roll the wire to cover the entire insulating set. However, do this carefully because you want the wire to remain intact. You might need to bend the wire to make insulation removal easier.
Stripping for Scrap

Caption: An electrician stripping a wire
If you have a vise, mount it and position the wire inside. Use clamps to hold it firmly, which allows you to use both hands.
Next, get a sharp blade and slice the insulation. You don’t need advanced protective equipment, but gloves might be helpful. Additionally, make sure to get a blade with flat edges to make the cutting easier. You want to pull the insulation away from the attachment of wires. Once you start cutting, you can pull the insulation to remove it quickly.
Use an Abrasive Surface for Magnet Wires
The experts recommend using fine-grit sandpaper. You need to cut enough to wrap the wire’s end. Next, squeeze the sandpaper with your hand while pulling the wire with the other hand. You’ll need to rotate and keep pulling until you remove enough coating. If you don’t have sandpaper, emery boards can be an alternative.
Conclusion
You can pick from various insulation materials available. Therefore, it’s all about fitting the choice to your application. If you need help with your cable assembly, don’t hesitate to contact Cloom. Our experts are ready to assist, suggest, and deliver the best solutions for your wiring!