A wire harness is a cable assembly that transmits electrical power. Here, the manufacturing process provides the basis for the assembling of other electrical products. Harnessing includes cutting, soldering, stripping, also a wide range of cable assemblies. Moreover, it maximizes the process by binding the individual wires together. The process ensures safety and security as well as quality. Let’s go into the wire harness manufacturing process in detail.
Table of Contents
- What Is A Wire Harness Manufacturer?
- Basic Steps in Wire Harness Manufacturing Process
- Top 6 Defects during Wire Harness Manufacturing Process
- Conclusion
What Is A Wire Harness Manufacturer?
A wire harness maker could be a business or company. Furthermore, it helps in the assembly process to complete its production respectively.
The standard that companies follow for wire harness fabrication is IPC-620 certification. Thus, the IPC certified harness creator provides training to the people to meet the criteria. For wire harness production, the IPC-620 standard prescribes the best practicing approach.
Basic Steps in Wire Harness Manufacturing Process
The harness process follows mainly four steps.
Step 1: Design
Think about the box panel of wires hidden in the belly bottom of a motorbike or a cable assembly hidden behind a refrigerator; these all transmit energy. Engineers solve complex problems by following a design process daily related to electrical requirements and for human comfort. In addition, a lot of challenges arise about (electronic part) custom designs. In this regard, engineers choose industrial equipment.
For every part of construction in the industry, the priority is to customize a good design for your project.
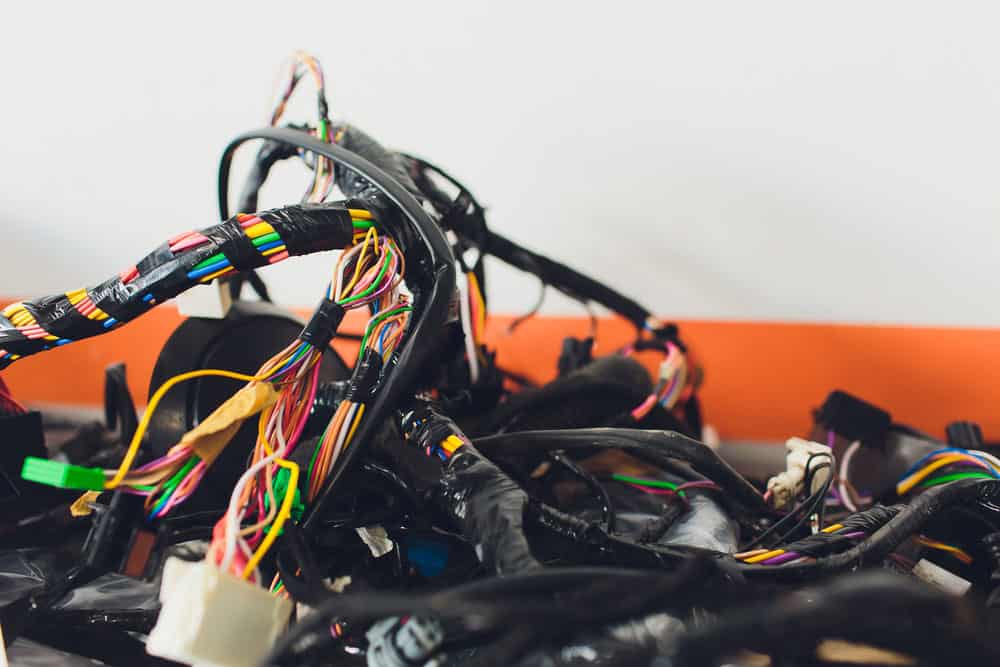
Caption: A Typical Car wiring system
Step 2: Prototyping
For optimal performance, an engineer needs to design a wire harness prototype model. In this way, he can check the ideal working of the wire assembly. For instance, if any abnormal issue occurs, it can be overcome coming into ground reality. A prototype is a perfect model which enables to achieve the maximum efficiency for an accurate model.
A prototype should reflect the main idea. All the information and ideas should be there at first. After, that an actual model can be achievable.

Caption: Breadboard for prototyping
Step 3: Production
It is necessary to optimize the errors for the cable assembly board. As assembly automation is the next generation, it’s spreading worldwide. So, the workforce is getting fewer. Although, some parts are involved in manual production. For which human resources are necessary, and it remains more cost-effective. One more reason that manual processes remain a primary section. Such that in few operations, automation cannot take over human craft. Cable harnesses also must protect wires from potential damages that lead to issues such as loose wires.
Wire Cutting
In a typical wire harnesses process, the initial step requires cutting the electrical wire to the precise length needed for your custom design. It is the most critical step in the process. Thus, assemblers perform it using the wire-cutting machine. Also, an automated machine cuts the wire to the given standards set by the builder.
Wire Layout
The second step involves designing a layout for the type of wire. Once the cables are organized, the assembler holds the cables with a cable clip.
Stripping and Connections
Proper stripping is necessary for appropriate connections. Practicing is essential for crimping terminals and connectors together and joint well for further operations as it makes wiring assembly smoother.
Assembly
At last, for design details, wires are combined into a harness to use for cable assembly. Manual production is necessary for the group of cables. And after joining, do tapping where necessary. Terminals need to be crimped onto wires. After that, many cables need to be connected to one terminal, performing crimping multiple times. Also, a few primary operations serve manually, such as fastening the tape for holding wires together, cable ties, or clamps.

Caption: Production Worker while assembling
Step 4: Testing
After completing the wire harness assembly process, electrical safety testing operations are carried out to satisfy the above 3-steps. Testing is the last yet crucial step for ensuring the reliability matches 100%. Final inspection in the cable harness includes:
- Pull tests
- Testing the continuity
- A megohm test
- Final appearance test under magnification
Remember that the manufacturers may put forward a few changes after performing these tests if the system does not meet quality standards.

Caption: Electrician while testing
Top 6 Defects during Wire Harness Manufacturing Process
Wire harnessing the manufacturing process requires intense care and attention, and any defect that occurs during production can sum up into a complete failure. Therefore, bringing an idea towards a defect-free wire harness production is nearly a plus point.
Incorrect Wire Preparation
Wire preparation is a sensitive section, needs proper care and sheer attention. Otherwise, it can affect the whole process. Many builders choose the wrong wire for preparation, cut, and strip for electrical connection goes all in vain otherwise.
Not Following the Assembly Drawing
In case any such abnormality occurs during the process. It will not only affect the cable assembly, but a rework cost will also add up.
Defects in Crimping
According to the harness maker, it’s the most critical step if not executed the right way. Because of this, short-circuits can prevail, and hence lives can go in danger.
Improper Soldering
Improper soldering can cause thermal damages hence cannot be ignored in any means when operators should set the standards for soldering, including precise equipment, standard temperature value, and timely inspections. Moreover, wire harness companies should use a good soldering iron.
Missing Wires and Using Wrong Hardware
In a hurry to finish the task on time, some producers miss a few stripping and connections. Hence, it could affect the whole wire harness assembly, which is crucial. Also, wire harness manufacturers may use the wrong hardware, which includes:
- Standoffs consisting of a barrel, wall screw, and a cap
- Versatile tools like a clamp
- Fastening components like washers or screws.
Improper Wire Tying
Last of all, in this process, manufacturers tie the wires for holding purposes. Sometimes due to excessive force, operators connect the cables too tight that it damages the wire. On the other hand, loose connections can lead to uneven tying. Thus to negotiate with any such defect, producers should tie the wires suitably.

Caption: Photo Electric Device
Conclusion
Wiring harness fabrication process growing challenges as harnesses get more complex. Also, the legacy methods of harness and construction are changing quickly. The changes must meet the customer’s requirements, and wire harness builders can satisfy the customer’s needs. Here at Cloom, we offer high-quality wire harnessing and cable connection. So, to get your quote, contact us now.